Frequently Asked Questions
There are fresh solutions and tips being added every week.
If your question or answer does not appear here, submit your enquiry here
V-TUF Pressure Washers
Q: My pressure washer has poor water flow and pressure or is not spraying at all.
A: IMPORTANT: Make sure that the pressure washer is turned off and that the pressure in the line has been released before proceeding with any servicing.
- Check that the pressure adjuster on the unloader valve is set correctly. The pressure should increase when your turn the adjuster clockwise and reduce when the adjuster is turned anti-clockwise.
- Check that the nozzle is not blocked. You can detect this by looking for a change in the shape of the water jet or checking to see if there is anything stuck in the nozzle orifice. You can clear the nozzle by pushing a probe through the nozzle orifice in the opposite direction to the normal flow of water then detach the lance from the gun and back flush the nozzle to remove any debris.
- Check that water filters are clean.
- If the pressure washer is sucking its water supply, make sure that the suction line has no air leaks. Generally, it is better to use a screw fitting for water suction because quick-release couplings are designed to work under pressure and will allow air in if used for suction. When air gets into the pump it reduces the compression and in turn, reduces the pump’s ability to pressurize the water.
- It is recommended that you get a pressure washer engineer to do this one. Check that the valves in the pump head are clean and not wedged open with debris. If debris is found in the pump, it is good to flush it through with water whilst the valves are out. Refit the valves ensuring that the o’rings are correctly placed.
- Hot water heating coils can get scaled up and restrict the flow of water. It is recommended that you ask a pressure washer engineer to descale your machine or replace the coil.
- Check that the high-pressure hose or trigger is not blocked or damaged.
Q: How often should i get my commercial pressure washer serviced?
A: It depends on the use of the machine, but generally, we recommend that it is serviced every 6 months if it is used on a daily basis. For ad-hoc use, a service every 12 months should be sufficient. It is important to regularly check the level and colour (Should not be milky) of the oil in the pump and ensure that any filters are clean. It is also important to ensure that your pressure washer is not exposed to frost or left idling when not in use.
Q: What oil can i use with my pressure washer?
A: It is important to refer to the manufacturer’s recommendations but generally 15W40 oil will suffice. To enhance the life and performance of your pump and reduce heat and friction, we highly recommend V-TUF PL500
Click HERE TO WATCH THE VIDEO
Q: What external water supplies can be used with my pressure washer?
A: For pressure washers with a flow of 15 litres per minute or less a standard 15mm mains tap water supply is the best way to supply your pressure washer. If your pressure washer flow rate is higher than 15 litres per minute, it is better to feed your pump from a header tank or suction from a bowser so that your pump is not starved of water. If your pump is staved of water it will cause cavitation (Cavitation happens when bubbles form within a fluid. When the bubbles experience higher pressures they collapse. This creates mini shockwaves that will eventually make tiny holes in the mechanics of the pump (pitting).
If the pressure washer is sucking its water supply, make sure that the suction line has no air leaks. Generally, it is better to use a screw fitting for water suction because quick-release couplings are designed to work under pressure and will allow air in if used for suction. When air gets into the pump it reduces the compression and in turn, reduces the pump’s ability to pressurize the water.
Q: Which nozzle do I need?
A: The size of your pressure washer nozzle is critical to ensure that you get the optimum performance out of your pressure washer without overloading the pump and motor.
To match the right size nozzle for your pressure washer, find out the recommended working pressure and flow rate of your pressure washer and use this V-TUF NOZZLE SIZE REFERENCE CHART
Q: Why is my tufFOAM spray gun no longer working and how can I fix it?
A: Through frequent use, sometimes the nozzle/gauze on the tufFOAM spray gun can become blocked and no longer output spray. If this happens, follow the below steps to rectify the issue:
- Remove u clip (1.)
- Remove yellow end (2.)
- Pull the grey section (3.) from the Control section (6.)
- Slide the nozzle section out (4.)
- Poke the gauze out using a small drill piece or Screwdriver (5.)
- Rotate gauze (5.) and put back in nozzle section (4.)
- Put back together.
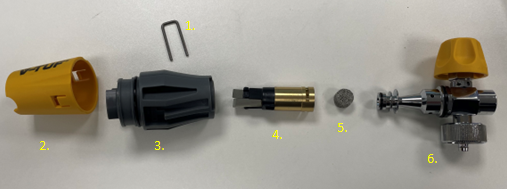
Q: Oil is leaking, what can i do?
A: The most common causes for the pump oil to leak are as follows:
- The oil has been overfilled. Check it by letting the pump cool down and checking the dipstick or the sight glass to make sure that the level of oil in the pump is correct. To resolve drain the excess oil so till the level is correct.
- The travel plug has not been replaced with the breather plug. To resolve this, replace the travel plug with the recommended breather plug (normally supplied with the pressure washer in a separate clear bag).
- Water is getting into the pump crankcase and causing the oil level to go up. Check the colour of the oil, if it is milky, it is proof that the oil is emulsifying. To resolve: It is very important to stop using your pressure washer and get an engineer to service the pump because the emulsified oil will lose its effective lubrication and will increase the friction and heat within the pump which will cause the pump to overheat and cease.
- The oil seals are worn out. You can check this if the oil is dripping out of between the crankcase (Normally cast Iron) and the pump head (Normally brass). To resolve: It is very important to stop using your pressure washer and get an engineer to service the pump because a reduced level of oil will increase the heat of the pump which will cause the pump to overheat and cease. Oil acts as a coolant as well as a lubricant.
- The oil drain plug is not sealed. You can check this if the oil is dripping out of the drain plug at the bottom of the pump. To resolve this, check that the seal is in place and tighten the plug. Wipe the oil sill away and check to ensure that the leak has stopped. Check that the oil level in the pump is correct. A reduced level of oil will increase the heat of the pump which will cause the pump to overheat and cease. The oil acts as a coolant as well as a lubricant.
A: The most common causes for your pump to overheat are as follows:
- If the pressure washer has been left idling, the water in the bypass system will heat up and eventually cause the pump to overheat and fail. It is important to turn your pressure washer off the mains power connection when it is not in use. This will increase the working life of your pressure washer, save energy, and prevent damage.
- Water is getting into the pump crankcase and causing the oil level to go up. Check the colour of the oil, if it is milky, it is proof that the oil is emulsifying. To resolve: It is very important to stop using your pressure washer and get an engineer to service the pump because the emulsified oil will lose its effective lubrication and will increase the friction and heat within the pump which will cause the pump to overheat and cease.
- The unloader valve is set too high. This caused the pump to overload (go into bypass) at a higher pressure. To resolve, pull the trigger and run the pressure washer whilst unwinding the pressure valve. Keep doing this until you notice that pressure starts to drop. The optimum setting is right at the point where you feel the pressure start to drop. Lock in this position. It is recommended that you get a competent engineer to check your setting.
Q: Can i use my pressure washer with salt/sea water?
A: Sea/Salt water is corrosive to many metals including brass. If you are needing to use sea/salt water through your pressure washer it is recommended that you use a stainless pump head. These are very rare and expensive. A cheaper alternative would be a nickle plated brass head. You must also take into account the other metals that the water will come in contact with. For instance the pistons, filters, unloaders valces etc. All V-TUF pump heads come with nickle plated pump heads as standard. It is recommended that pressure washers only use fresh water for best results and pump life. Other types of water could cause the pump systems to wear out quicker or void warrantee.
Q: What oil do I use in my pressure washer pump?
A: V-TUF use PL500 as this extends the life of your pump and reduces running temperature and wear.
Q: How often do I change the oil on the pressure washer pump?
A: It is dependant on the use of your pressure washer. As a guide, if your pressure washer is used 5 hours a week or more we recommend that use change your oil every 6 months. If its used less than 5 hours a week change once a year. We do recommend that you check the oil level and colour before use. If the oil level is low top it up and check for any sings of leaking. If the oil level it too high, drain some out. If the oil is a milky colour, it could mean that your water seals have worn and the water is mixing with the oil. If this is the case, get your pressure washer serviced before further use.
Q: Are pressure washer hoses and lances covered by warrantee?
A: They are covered for manufacturing defects but not general wear and tear. They are regarded like tyres on a car. The more they are used the sooner they will wear out.
Q: What is the difference between the max pump rated pressure and the operating pressure for my pressure washer:
A: The max pump rated pressure is what the pump has been designed to accommodate. V-TUF uses over size pumps so that pumps run well within their limits to enhance the reliability and safety of the pressure washer.
The max operating pressure is what the pressure washer will produce. This is tuned to the V-TUF UK OPTIMAL STANDARD (The sweet spot of Flow, Pressure, Amps). The UK OPTIMAL STANDARD optimises the performance and reliability of your pressure washer.
Q: How do i get my RAPID VSC Hot to suck water from a water butt rather than be fed from a tap?
A: WATCH https://fast.wistia.com/embed/medias/s5jexiib8g
A: Sea/Salt water is corrosive to many metals including brass. If you are needing to use sea/salt water through your pressure washer it is recommended that you use a stainless pump head. These are very rare and expensive. A cheaper alternative would be a nickle plated brass head. You must also take into account the other metals that the water will come in contact with. For instance the pistons, filters, unloaders valces etc. All V-TUF pump heads come with nickle plated pump heads as standard. It is recommended that pressure washers only use fresh water for best results and pump life. Other types of water could cause the pump systems to wear out quicker or void warrantee.
Q: What oil do I use in my pressure washer pump?
A: V-TUF use PL500 as this extends the life of your pump and reduces running temperature and wear.
Q: How often do I change the oil on the pressure washer pump?
A: It is dependant on the use of your pressure washer. As a guide, if your pressure washer is used 5 hours a week or more we recommend that use change your oil every 6 months. If its used less than 5 hours a week change once a year. We do recommend that you check the oil level and colour before use. If the oil level is low top it up and check for any sings of leaking. If the oil level it too high, drain some out. If the oil is a milky colour, it could mean that your water seals have worn and the water is mixing with the oil. If this is the case, get your pressure washer serviced before further use.
Q: Are pressure washer hoses and lances covered by warrantee?
A: They are covered for manufacturing defects but not general wear and tear. They are regarded like tyres on a car. The more they are used the sooner they will wear out.
Q: What is the difference between the max pump rated pressure and the operating pressure for my pressure washer:
A: The max pump rated pressure is what the pump has been designed to accommodate. V-TUF uses over size pumps so that pumps run well within their limits to enhance the reliability and safety of the pressure washer.
The max operating pressure is what the pressure washer will produce. This is tuned to the V-TUF UK OPTIMAL STANDARD (The sweet spot of Flow, Pressure, Amps). The UK OPTIMAL STANDARD optimises the performance and reliability of your pressure washer.
Q: How do i get my RAPID VSC Hot to suck water from a water butt rather than be fed from a tap?
A: WATCH https://fast.wistia.com/embed/medias/s5jexiib8g
V-TUF Vacuum Cleaners
Key Vacuum performance measures:
Q: What is CFM?
A: CFM is a volumetric measurement and stands for Cubit Feet per Minute.
There are 0.00047194745 Cubic Metres per Second in one CFM.
Q:How many Cubit Feet per Minute in one Litre per Second?
A: 2.1188799727597
Q: How do I convert airflow velocity (i.e. Metres per Second) measurements into a volumetric measurement (i.e Metres Cubed per Second)
A: You will need the duct dimension and use a reputable tool like this. https://www.hse.gov.uk/lev/calculator.htm#volumeflow
Once you have calculated the velocity to volumetric you can simply use a calculation to convert it into further units of measure.
Air Change Rate
Air Change Rate is an important calculation for ventilation and air quality applications.
Use the following tool to ensure that your equipment has sufficient performance for your application.
https://www.hse.gov.uk/lev/calculator.htm#airchangerate
Q: Do i need to use V-TUF multi motor vacuums cleaners on a larger that standard power supply?
A: All V-TUF 240 volt triple motor vacuum cleaners are set up to run on a 13amp 240 Volt supply.
Key Vacuum performance measures:
Q: What is CFM?
A: CFM is a volumetric measurement and stands for Cubit Feet per Minute.
There are 0.00047194745 Cubic Metres per Second in one CFM.
Q:How many Cubit Feet per Minute in one Litre per Second?
A: 2.1188799727597
Q: How do I convert airflow velocity (i.e. Metres per Second) measurements into a volumetric measurement (i.e Metres Cubed per Second)
A: You will need the duct dimension and use a reputable tool like this. https://www.hse.gov.uk/lev/calculator.htm#volumeflow
Once you have calculated the velocity to volumetric you can simply use a calculation to convert it into further units of measure.
Air Change Rate
Air Change Rate is an important calculation for ventilation and air quality applications.
Use the following tool to ensure that your equipment has sufficient performance for your application.
https://www.hse.gov.uk/lev/calculator.htm#airchangerate
Q: Do i need to use V-TUF multi motor vacuums cleaners on a larger that standard power supply?
A: All V-TUF 240 volt triple motor vacuum cleaners are set up to run on a 13amp 240 Volt supply.
- All V-TUF 110 volt twin motor vacuum cleaners are set up to run on a standard 16amp 110 Volt supply.
- Note: Some areas suffer from a fluctuating grid power supply. This will affect the standard operation.
V-TUF Warranty and Returns
Q: What warranty do V-TUF Offer?
A: Where there has been a failure due to product or manufacturing defects, a free-of-charge rectification or replacement will be issued.
Q: How long is my V-TUF product covered under warranty?
A: For 12 months following the date of purchase.
Q: Can I Return my V-TUF Product?
A: V-TUF are keen to deal fairly with our customers so we review each request on it own merits, guided by section 7. Return of Goods in our trading terms
Q: Can I get my V-TUF product repaired?
A: Yes, simply send an email with details of your machine, what needs to be done and your address to enquiries@v-tuf.com
Q: Are field engineers available?
A: Yes, following a virtual assessment, V-TUF can arrange for an engineer to attend to a product in the field. Alternatively, you can use our service agent locator to find the nearest service engineer to you and contact them directly.
Q: For Dealers, does the warranty on the components V-TUF supply pass on to our customers in the event that there is a mechanical fault?
A: Yes, warranty is still covered after the product has been sold to the customer.
Q: What warranty do V-TUF Offer?
A: Where there has been a failure due to product or manufacturing defects, a free-of-charge rectification or replacement will be issued.
Q: How long is my V-TUF product covered under warranty?
A: For 12 months following the date of purchase.
Q: Can I Return my V-TUF Product?
A: V-TUF are keen to deal fairly with our customers so we review each request on it own merits, guided by section 7. Return of Goods in our trading terms
Q: Can I get my V-TUF product repaired?
A: Yes, simply send an email with details of your machine, what needs to be done and your address to enquiries@v-tuf.com
Q: Are field engineers available?
A: Yes, following a virtual assessment, V-TUF can arrange for an engineer to attend to a product in the field. Alternatively, you can use our service agent locator to find the nearest service engineer to you and contact them directly.
Q: For Dealers, does the warranty on the components V-TUF supply pass on to our customers in the event that there is a mechanical fault?
A: Yes, warranty is still covered after the product has been sold to the customer.